By Justin Chandler
When Stephania Stefanakou started 3D printing fashion, nobody else at Ryerson was doing it, she said.
Now, the fashion communication graduate uses 3D printing to make clothes for her business.
Stefanakou works at Ryerson’s Fashion Zone and Design Fabrication Zone (DFZ).
Both are programs that provide space, resources and mentorship to people starting businesses. She also works at the Digital Media Experience Lab (DME), where people can work with design technologies like 3D printing—a process in which layers of material are formed under computer control to create objects.
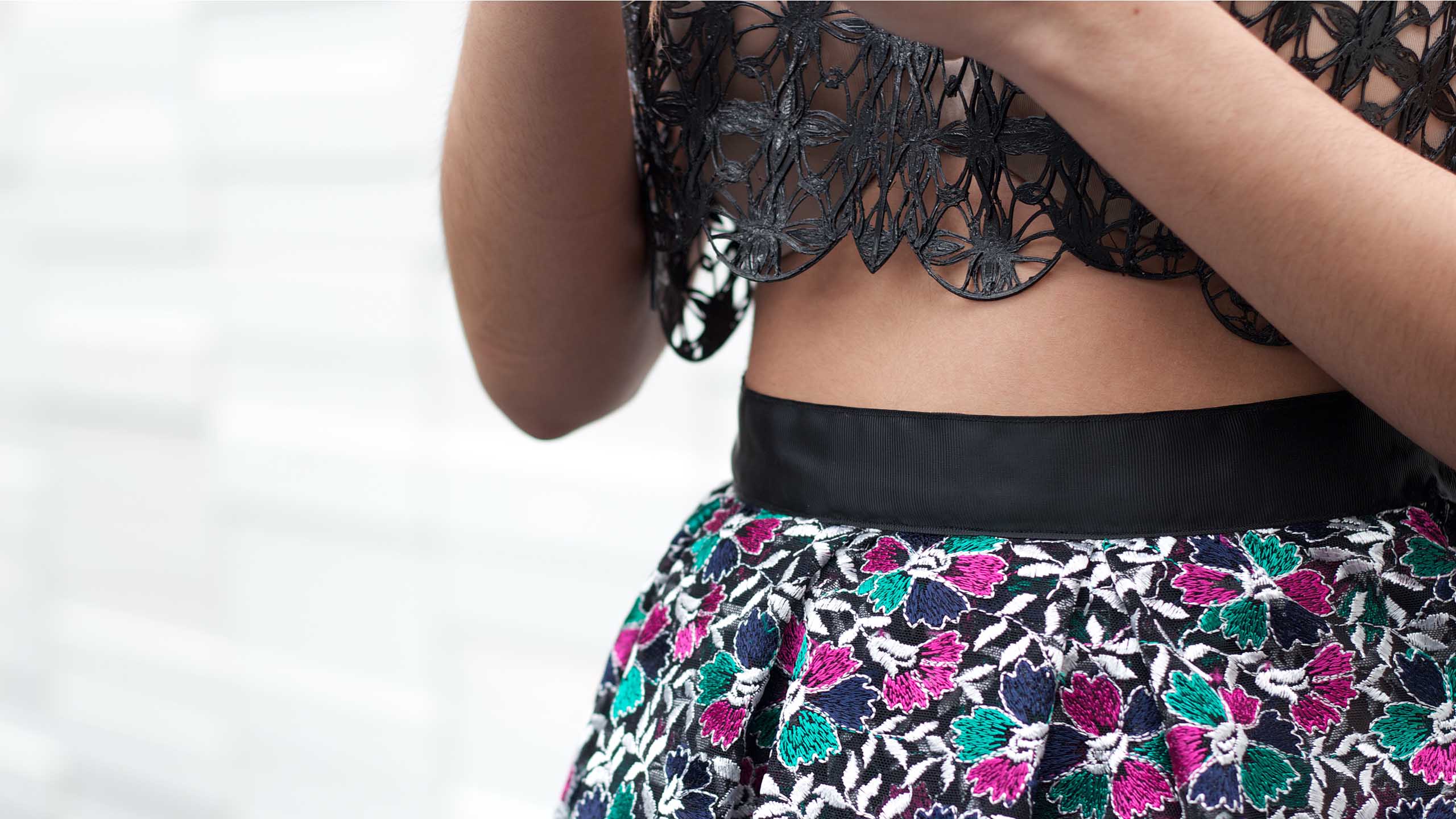
Photo: Leen Al-Taher
Stefanakou designed and created a 3D-printed black, lace-like crop top for her thesis project before graduating from the fashion communication program in 2016. On March 23, the Faculty of Communication and Design awarded Stefanakou $500 for her project.
She also made a skirt that complements the top. It changes shape using material that curls up when heated to 40 C and lengthens when cooled to 15 C.
Stefanakou said she likes to experiment and test the limits of the technology when she uses it.
When Stefanakou conducted research for the first shirt she made, she found “people weren’t too open to the idea of wearing plastic. Because that’s what they think 3D printing is.”
Stefanakou said that really, 3D printing technology has advanced enough that one can use almost any material and create fabric out of it. It’s not just printing PLA, which is the basic plastic many people use.
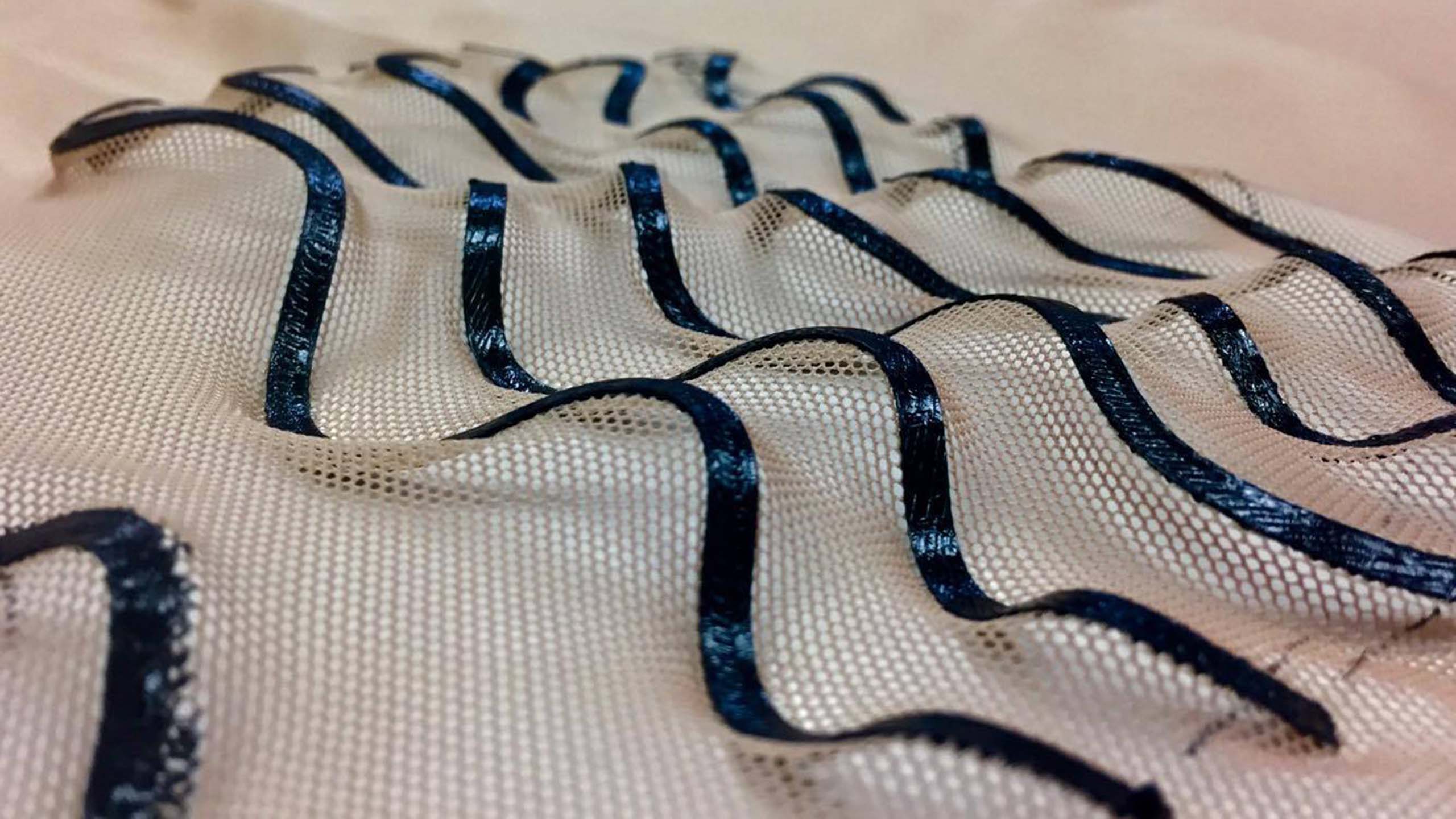
Photo: Stephania Stefanakou
Instead, Stefanakou uses thermoplastic elastomers (TPE), which are used in active wear and rain coats. One can print anything that can melt and go back to a solid form when it cools, she said.
“When I 3D print TPE, it doesn’t feel like actual hard plastic. It feels and it looks like fabric. It sits really nicely on your body,” Stefanakou said.
When she started mixing 3D printing and fashion, Stefanakou found people were more receptive to 3D-printed designs on fabric than 3D-printed fabric, so she started there.
She said it took two months of testing combinations of different fabrics and printing settings to find fabrics and printed materials that would stick together. Nylon works well. Chiffon doesn’t.
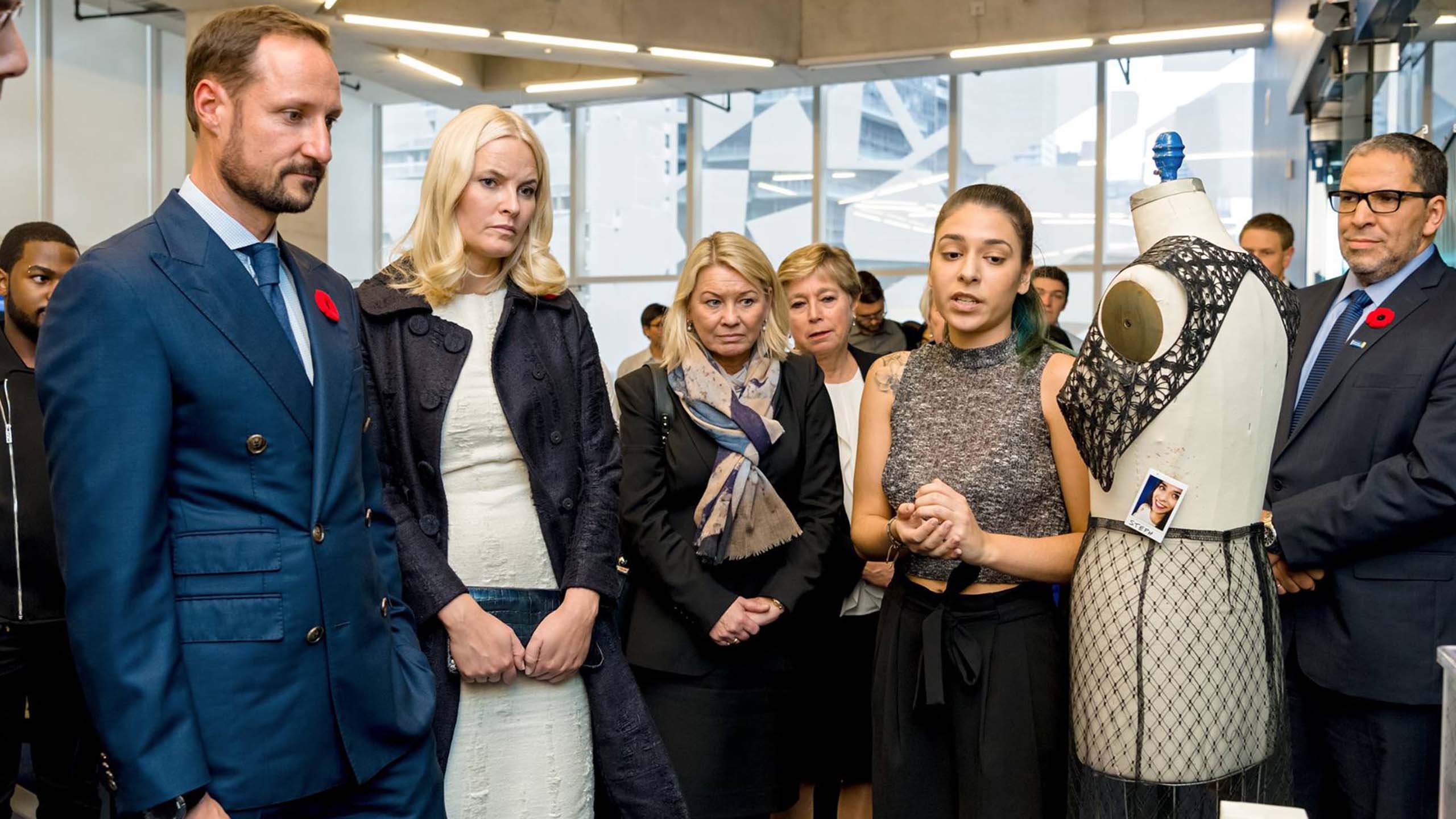
Photo: Clifton Li
When Stefanakou designs, she doesn’t make it apparent that her clothes are 3D printed. She wants that to be known, but not the first thing people notice.
She said people who are unfamiliar with the technology may not even realize her garments are made with it.
In her third year at Ryerson, Stefanakou participated in Re-Engineering Fashion—a competition that brought together business students, fashion students and engineers. That’s when she learned she’s interested in companies.
Stefanakou and four others created a business that won the competition.
House Of Anesi, the now two- year-old business, is part of Ryerson’s Fashion Zone. It produces bras that adapt to changes in breast-size, which can occur due to hormonal fluctuations or weight gain, Stefanakou said.
“Breast size can change very drastically, even in a year,” she explained, which means a person can go through multiple differently-sized bras in a matter of months. The bras at House Of Anesi can expand up to two inches—one cup size.
Stefanakou started work at the DFZ in the fall when the director offered to buy the 3D-printing equip- ment she now uses there.
Last month, she got equipment that will let her print with two dif- ferent colours, and with supports, which will allow her to make more flexible materials.
She said she learned a lot at House of Anesi and at her other business, STEFANAKOU, that she didn’t learn in the fashion communication program, such as how to manufacture products, develop a website, write funding applications and talk learn in the fashion communication to investors.
Leave a Reply